Press Release
Johns Hopkins APL Maker Community Crafting Face Shields for Medical Workers
As the world became aware of the shortage of personal protective equipment needed by health care workers on the front lines of the battle against COVID-19, it’s no surprise that many engineers and scientists from the Johns Hopkins Applied Physics Laboratory (APL) mobilized immediately.
For Sunita Bhatia, a supervisor in APL’s Force Projection Sector, and Michael Nord, a remote sensing scientist in APL’s Asymmetric Operations Sector — members of the Lab’s informal community of makers — that meant activating their network and starting conversations over email.
Bhatia saw an email asking if anyone had a list of the Lab’s 3D printers. “That’s where the power of APL’s network comes in,” she said.
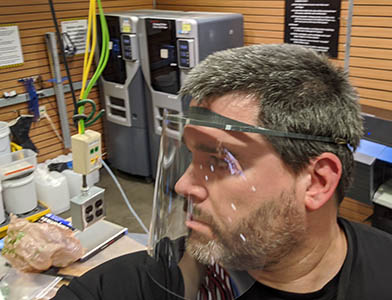
Credit: Johns Hopkins APL
As a longtime member of the Lab’s maker community, Bhatia has trained colleagues on 3D printing machines in APL’s maker space, Central Spark, for years. Central Spark is a collection of connected innovation spaces with a wide variety of specialized equipment staff can use for both official and personal work any time. Bhatia reached out to Bob Matteson, supervisor of the Advanced Mechanical Fabrication Group in APL’s Research and Exploratory Development Department, who put her in touch with Michael Boyle, another REDD supervisor, who was helping organize the Lab’s efforts around PPE production.
The conversation grew, and eventually, the team decided on a couple of different designs and began printing.
“I’m most familiar with 3D printers, so the headpieces for face shields seemed like an obvious thing for me to start with,” Nord said.
Nord went to the Lab’s main maker space with some files he found online for the headpiece of a face shield, as well as a design Bhatia received from a family member in New York, and fired up one of the Lab’s 3D printers.
He printed about a half dozen but quickly realized there were flaws in the original designs. A typical 3D print involves building layers of plastic, but to ensure the shape, you need a support material to keep the design intact throughout printing. After the printing finishes, you submerge the print in sodium hydroxide, which dissolves the support material.
“This is why you do rapid prototyping,” Nord said. “Sodium hydroxide is something you don’t want leaching out of the plastic near your face or eyes. So in this case, where we were purposely printing something to be worn on the face, I had to come up with something that needed minimal support material to avoid having to use the sodium hydroxide.”
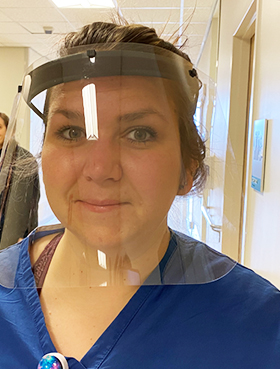
Credit: Karen Boyle, The Johns Hopkins Hospital
There were other issues with the first few designs as well. One of the headpieces was really easy to print but tough to assemble. “If it takes an engineer an hour to process for assembly, it’s probably not the best design,” Bhatia said.
The team continued to iterate on multiple designs, and experimented with different types of plastic for the shield, such as transparencies (too flimsy), and different types of elastic for securing the shields to the wearer’s head (some were too tight).
“I’m a hobbyist. I don’t do this for a living,” Nord said. “But what I’m hoping is that we’ve iterated on the design enough that when it’s tested by medical professionals, they approve it and we can hand the designs over to a team at the Lab with really big printers who can churn these out much faster.”
Getting the face-shield prototypes into the field for evaluation was easy. Boyle’s wife, Karen, is a nurse at The Johns Hopkins Hospital. She brings the prototypes to work each time there are new versions to test. Last week, four copies of the latest version were so well received she had colleagues asking for more.
The team has continued to provide shields to Boyle for distribution at the hospital and has also ensured the design is possible for anyone with a 3D printer at home to help.